The requirements are high. “Our supply chain management has to be excellent because our business is very complex,” says Rupert Freutsmiedl, Director Supply Chain Management at Dr. Babor GmbH & Co. KG. 500,000 shipments per year, more than 1,000 products, many of which are regularly varied, ten distribution channels worldwide. And this with strong growth and in an industry that is increasingly regulated. “You can only do that with efficient supply chain management,” says Freutsmiedl. For the manufacturer of precision cosmetics Made in Germany, best-in-class processes are therefore simply a “business necessity”. Especially in these times, the shipping of premium cosmetic products to end customers is becoming strategically even more important for the family-owned company.
In the past, Babor was already able to rely on a fully automated labelling and carton sealing system in the dispatch department of the Aachen headquarters. When the plant was modernized in 2018, it was obvious to automate and integrate numerous processes related to shipping at the same time. For example, data exchange with external service providers such as logistics companies and customs processing should be carried out without media breaks in the future. “Shipping and customs from a single source, that was our clear goal,” reports SCM boss Freutsmiedl.
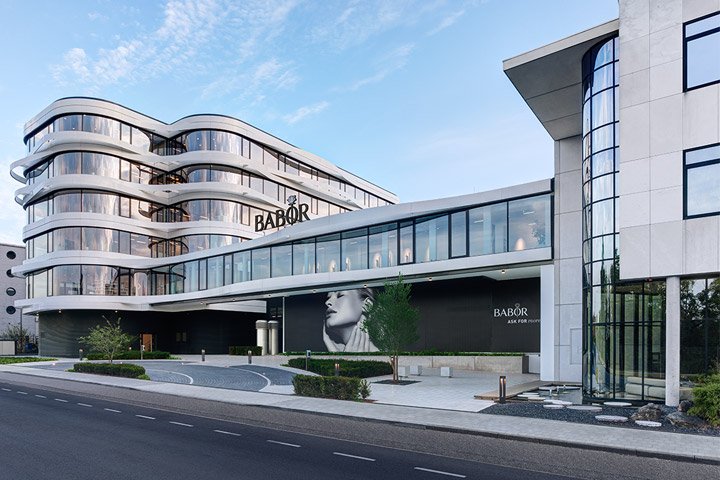
The project
For Babor, dbh implemented a comprehensive integration of the tariff, customs and shipping solution for an automated and smooth shipping process.
Benefits
- Less workload for many employees
- Legally compliant transactions
- Real-time data
- Improved customer service
Objective: Set a high standard and remain flexible at the same time
Together with an external consultant, two manufacturers were found who promised an appropriate solution. The logistics experts from dbh made the running, “because the chemistry was right and the solutions already have a very good range of functions in the standard package,” says Freutsmiedl. Babor’s clear goal was to deliver best practice in systems integration in the new shipping department and to develop an industry standard. At the same time, the special features of the Babor business were to be reflected.
Solution: an integrated shipping solution with many advantages
dbh implemented the solution at Babor based on the products Advantage Delivery (shipping), Advantage Customs (customs) and Advantage Compliance (tariffing). Babor’s desire for closer integration of the shipping and customs solutions beyond the previous integration required a reorganization of responsibilities. “It was an agile, organically growing joint development work in which both sides contributed very constructively,” Freutsmiedl reports on the good cooperation with dbh. Complex requirements from Babor were implemented very well, he says, even if they only turned out to be necessary after the fact. “Together with dbh, we have taken a big step forward,” says Freutsmiedl.
Thanks to the real-time connection of the shipping service providers, the labelling of parcels is now carried out “at a very high speed”, reports project manager Anna Offermann. After scanning the package, the label is printed within 2-3 seconds. Today, Babor’s largest mail order company is connected to Babor in real time, and shipment numbers are retrieved via web services. Babor exchanges number ranges with three other suppliers. dbh has also integrated a requirement from Babor here: The labels are colour-coded – depending on the logistics service provider.
The fact that the logistics service providers are integrated in the dbh solution as standard has the advantage that Babor is also aware of the shipping status at all times. If an end consumer or a cosmetics institute asks Babor about their delivery today, the sales department can give an immediate answer without having to look in third-party systems or even ask colleagues.
“The solution reduces the workload of colleagues while improving customer service.”
Anna Offermann, Project Manager Dr. Babor GmbH & Co. KG
The four employees in customs processing at Babor are also pleased with the integrated solution. Whereas in the past taxis were sent on their way with customs documents, today all documents for customs clearance are available online at Babor. “In addition to integration, this is also a concrete example of digitalization,” Freutsmiedl explains. Babor’s customs officers can now tariff deliveries and send the relevant paperwork on its way digitally with much less effort, and with different processes in one system: from individual parcels to the collective customs clearance of entire pallets. dbh has also implemented special requirements for Babor in the integration of customs issues. Switzerland, for example, requires the quantity of a certain ingredient to be stated. “The customs clearing agents can now effortlessly extract this information from the system,” project manager Offermann is pleased to say.
At Babor, confirmations of arrival are now travelling digitally instead of analogue. Whereas B2B customers used to confirm a delivery by printout, signature and scan, today they receive an e-mail with a link that only needs to be clicked on and is legally valid as an electronic signature. “Another big advantage,” Freutsmiedl finds. He and his colleague Offermann see the legal security of all processes as an important added value. Legal compliance is an integral part of all dbh solutions, he says, and it is reassuring to be able to rely on it – especially in a constantly changing legal environment.
It is also easier than ever for Babor to process all Intrastat information for the Federal Statistical Office. And with the freight cost module integrated into the shipping solution, the supply chain management in Aachen can now precisely check whether the freight service provider has billed correctly.
Further expansion planned
In a next step, Babor will connect not only parcel shippers but also its forwarders to the new “digital all-in-one solution”, announces SCM boss Freutsmiedl.
To ensure that supply chain management at Babor continues to maintain its top position, the family-owned company with its 600 employees has a lot planned. Following the successful introduction of dbh and an advanced planning system, the company is currently planning to introduce a warehouse management system.
At the same time, the beauty specialist is building a new central location for production and logistics in Eschweiler. The dbh solution will also be used there. “It was also a decision criterion for dbh that we could take our fully integrated solution and scale it,” says Freutsmiedl.
“Babor is ready for the future with its shipping system.”
Rupert Freutsmiedl, Director Supply Chain Management Dr. Babor GmbH & Co. KG
About Dr. Babor GmbH & Co KG
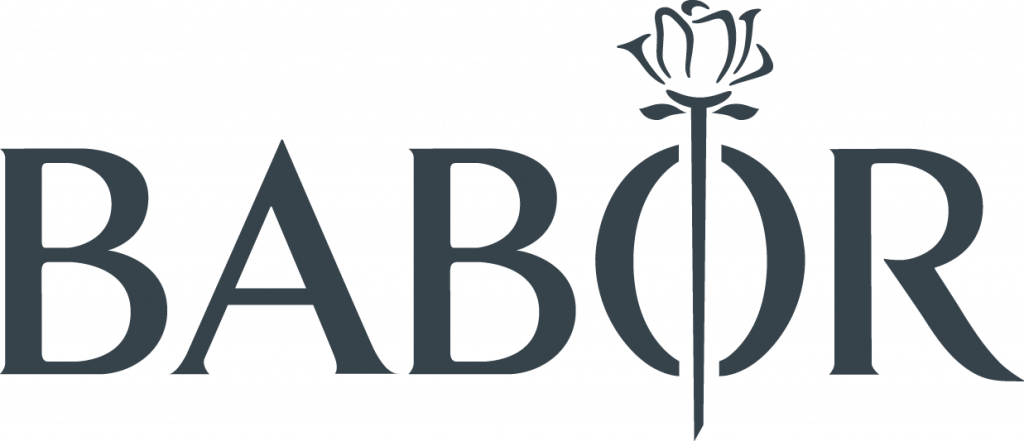
BABOR is a leading international brand of professional cosmetics and still a family business today. The company is headed by the third generation of the owner family.
To meet the demands of its customers, BABOR relies on more than 60 years of skin care expertise made in Germany: all development and production takes place exclusively at the company headquarters in Aachen. Therefore, every product from the idea to the finished jar is a promise of quality and stands for science, precision and effect.